Versatile, Affordable, Easy to Use
Robotic technology delivers real solutions for dispensing, gasketing, soldering, conformal coating, and more. Benefits include:
- Accelerated production output
- Improvement in tolerance precision and accuracy.
- Significant waste reduction.
- Improved worker safety.
New Precision Technology, Inc. is a leader in affordable standard and semi-custom automated systems. To learn more, give us a call at 412-596-5948, or visit our Contact Us today.
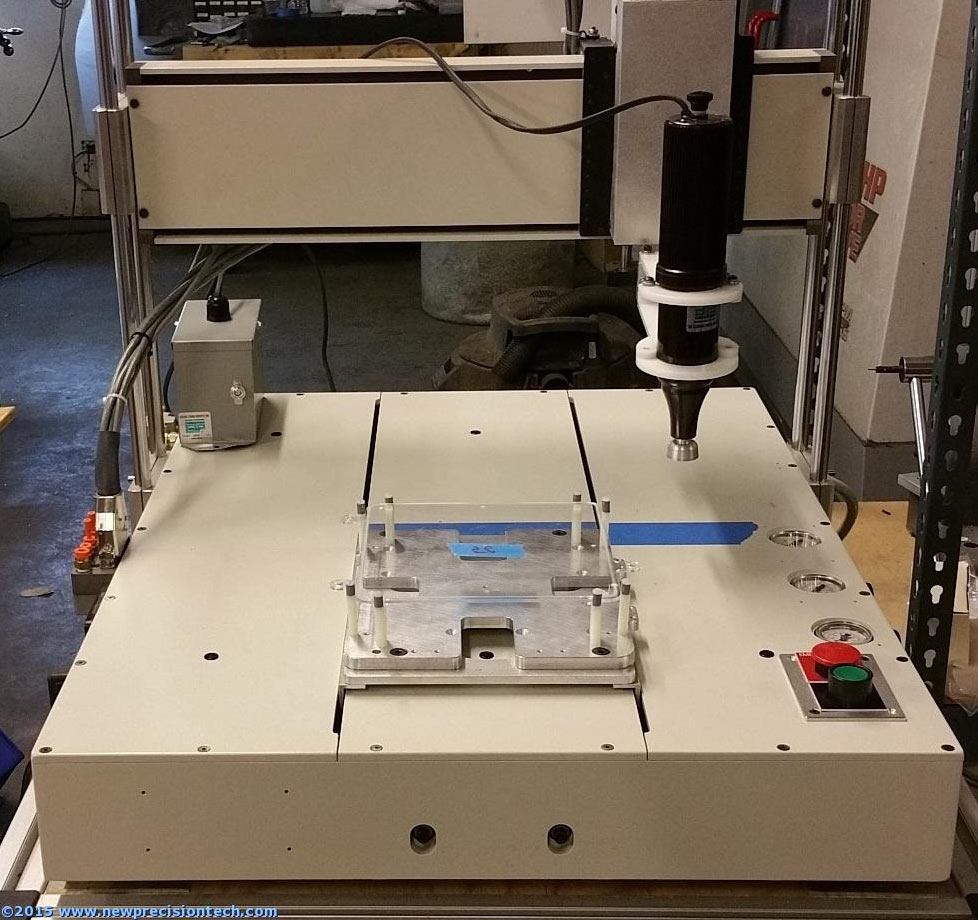
CP-16 Line
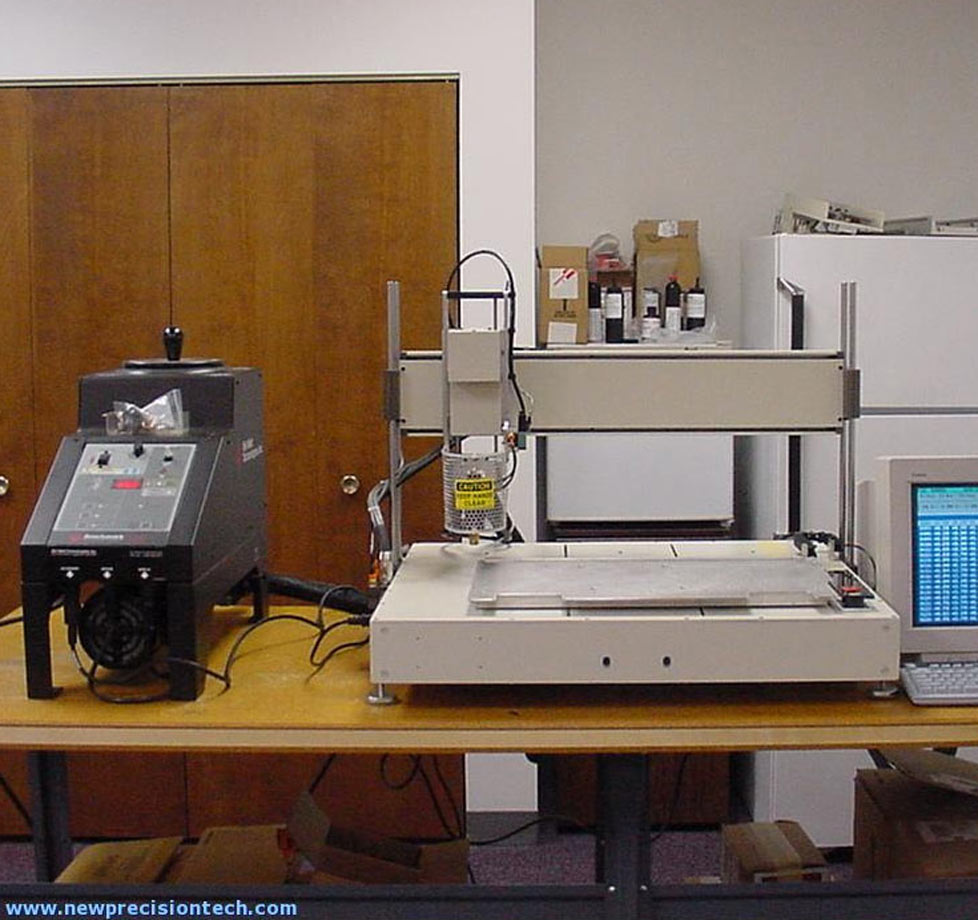
CP-24 Line
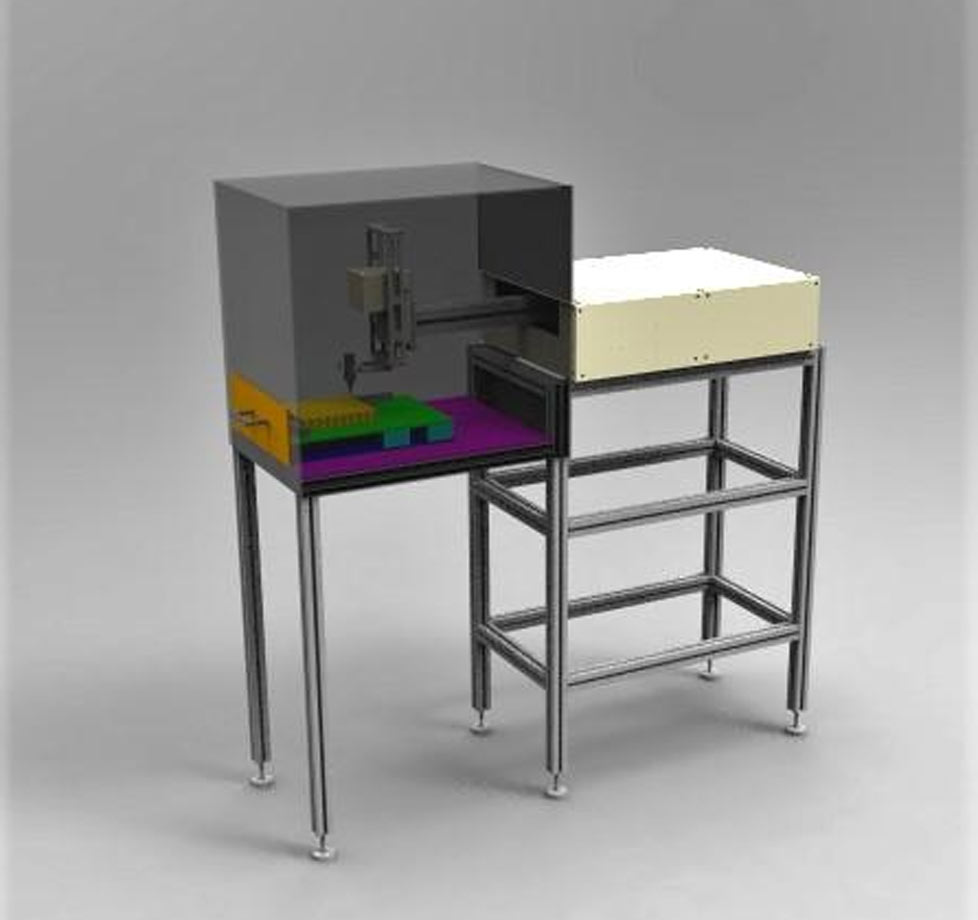
ICP Line
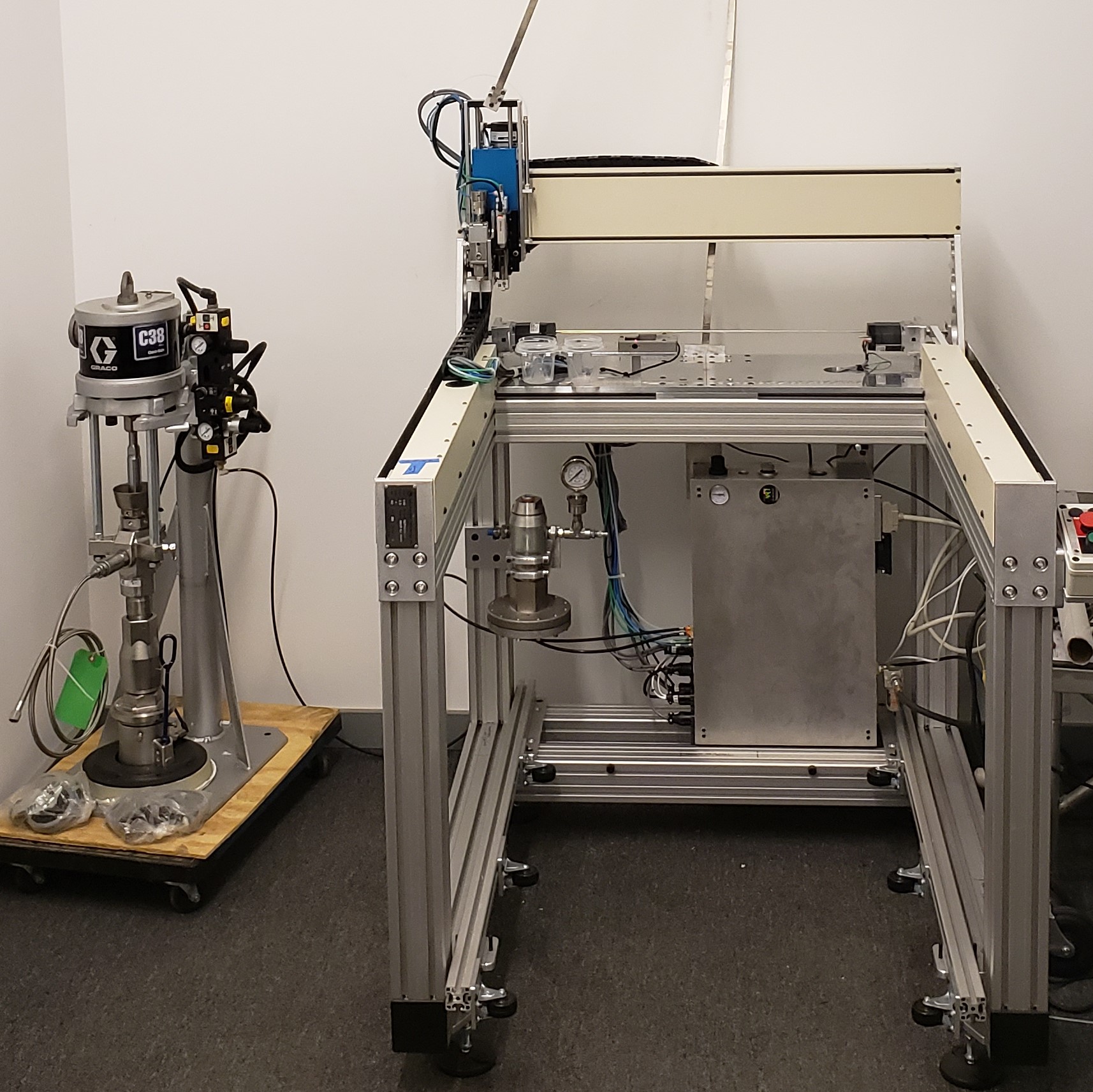
SCP Line
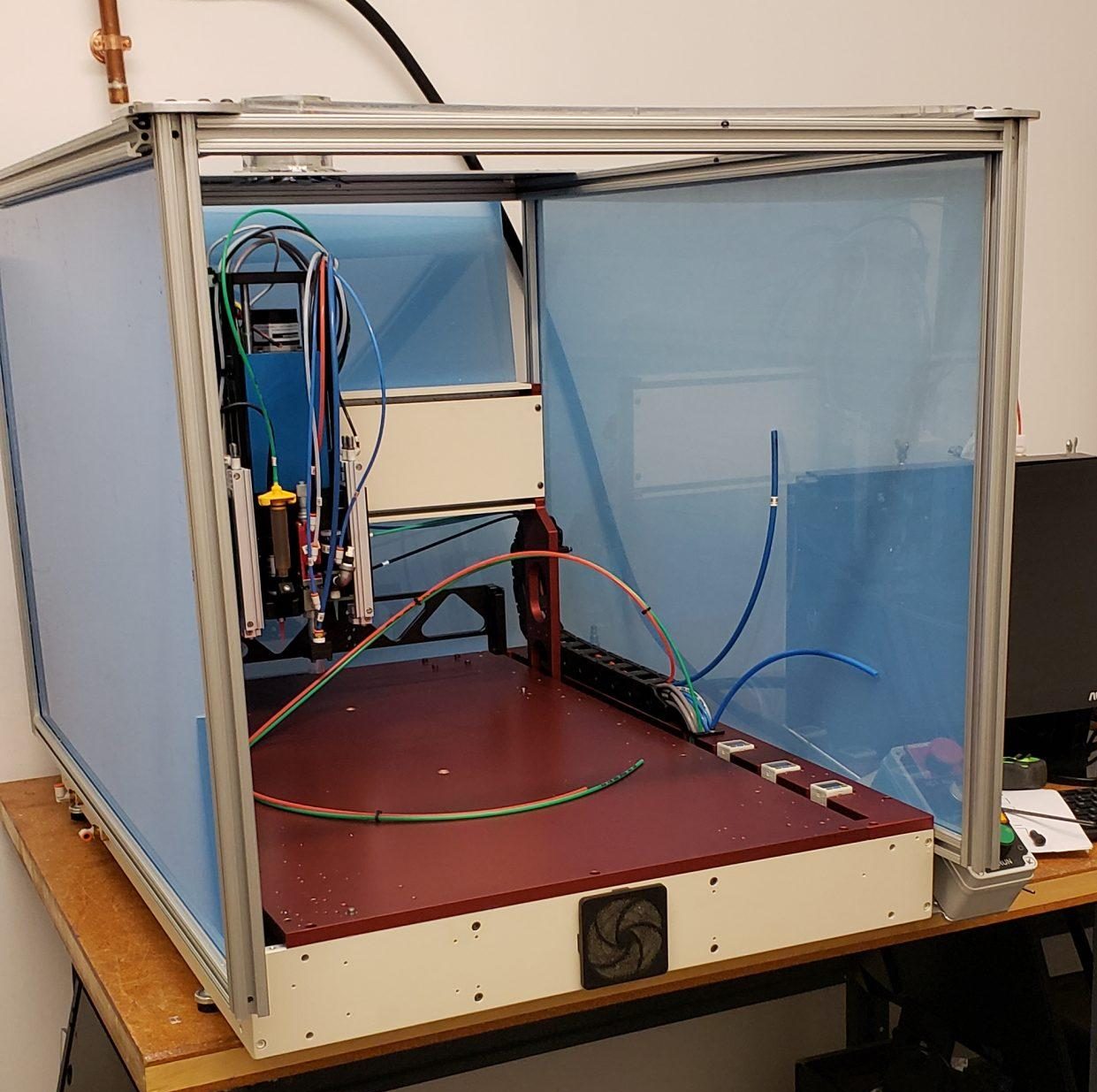
GCP Line
CP-16
The CP-16 is available in benchtop and stand-alone XYZ application solutions for electronics, biomedical, and general assembly. It can be configured as a Dispensing System, a Conformal Coating System, a Soldering System, or a Continuous Gasketing System.
Highly precise, the CP-16 can be used in doming applications, where a 3D effects in imparted to a 2D surface.
CP-24
At 24 inches per second of travel, this CP24 yields terrific throughput! The head dispenses "pats" of hotmelt PSA adhesive to help fixture products on a plastic sheet. The sheets are held on with a vacuum system that detects when a sheet has been removed and when a new sheet has been placed on the pallet.
The high speed and the vacuum system combine to yield a throughput rate of less than eight seconds per sheet!
ICP-Line
The ICP is our in-line model for working over conveyors or dials. This particular design has a number of advantages over competing systems:
The design has the characteristics of any cartesian versus SCARA multiple DOF arms - mainly that these minimize motor torque requirements.
In conjunction with item #1, the lower torque also means the bearing systems are subject to lower wear and tear, increasing system longevity.
The design completely encloses the motion elements, improving safety. The design reduces the typical batch load/unload cycle of seven seconds to something often as low as one second
SCP Line
Our SCP line is designed to work over carts that are pushed into the system. Heavy products are often moved through the factory on carts and the SCP can detect when a cart is "parked" in the machine and then dispense on the fixtured part.
We have a suite of sensors that can work in conjunction with the part to quickly remap product height and position and thereby resolve locating issues inherent in "cart" production.
These systems tend to be larger. cart systems start at 34" x 34" work envelopes and can readily go much larger. This platform is the first of our modular series and can yield work envelopes up to 50" in X and scales in 24" increments in Y. The addition of three sections in Y yields a 96" Y travel.
GCP Line
Our GCP line is our axis-on-axis design. It achieves the pinnacle of of accuracy as the X gantry and Y axis is all referenced from the same surface. Part weight becomes irrelevant (versus our CP line for example) as the part is no longer in motion..
With axis-on-axis designs, safety becomes a crucial concern as the axis loads are far more substantial than in an H bridge design such as our CP lineup. With this in mind - and unlike other such systems - the GCP base extends beyond the moving members. This makes it trivial to incorporate side guards and even complete enclosure system integration is simplified.
These systems are both scalable and flip-able! The system can be customized from 16" x 24" to 50" x 96" and beyond. The system can be inverted and mounted to work over conveyors and index tables. This GCP design has extraordinary flexibility..
High speed throughput
Some applications demand high throughput that traditional batch mode machines like NPT's CP systems cannot supply. To address this need, NPT's ICP systems can be married to a rotary indexer so that concurrent operations can be done. Operator load/unload no longer adds to the overall cycle time as parts are loaded/unloaded on a separate "leaf" from the dispensing work area. The rotary indexer can be outfitted with a grid fixture to allow flexible palleting options, and each "leaf" can address a process - UV cure stations, inspection stations, and even other dispensing stations. Modular design allows the user to add leaf operations over time, as the production environment dictates.
More advanced processes can be incorporated as well: automated part load and unload, scanning, and even integration with automated molding machines is possible.
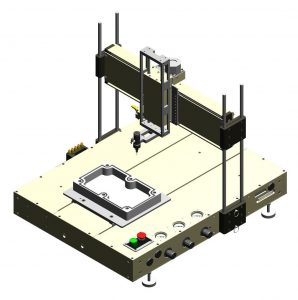
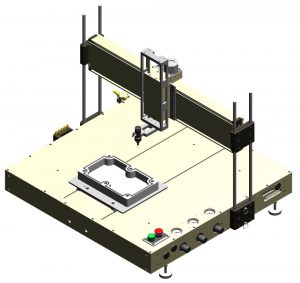
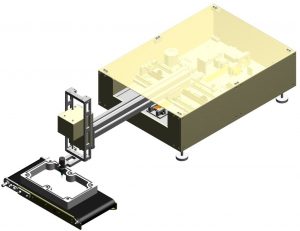
Two Component Cartridge Dispensing
New Precision Technology equipment can be outfitted to handle larger meter-mix heads for 2-part dispensing applications. A stronger z-axis stage, geared x-axis stage, and larger gantry shafts enable the use of heavier dispense hardware. A recommended needle tip calibrator will ensure that the necessary meter-mix tube replacements will stay on the mark every time. Dual-pack cartridge dispensing is a dispensing technique that avoids the breakdown and clean-up time of dedicated material lines.
Conductive inks and adhesives
Conductive ink, gasketting, and shielding applications benefit a great deal from the synergy of motion, sensing, and software. IMAGE ONE below shows traces formed with conductive inks on polyester with an LED placed directly on the ink to form the circuit. Subsequent application of a conformal coat serves to secure the assembly. Note the soldered wires on the polyester. Video one shows resistance traces precisely formed with the benefit of accurate height measurement. Video two shows sprayed RF shielding applied with minimal waste of material. Video three shows a silicone RTV filled with silver used as an EMI shield compound on cell phone housings.
Precision Gaskets For Fuel Cell Plates
Fuel cells can present interesting challenges when it comes to gasketing and sealing the spaces between plates. Stackup problems can become quite pronounced when multiplied by the number of plates in the stack. Well-defined specifications for fuel cells can simplify the process requirements.